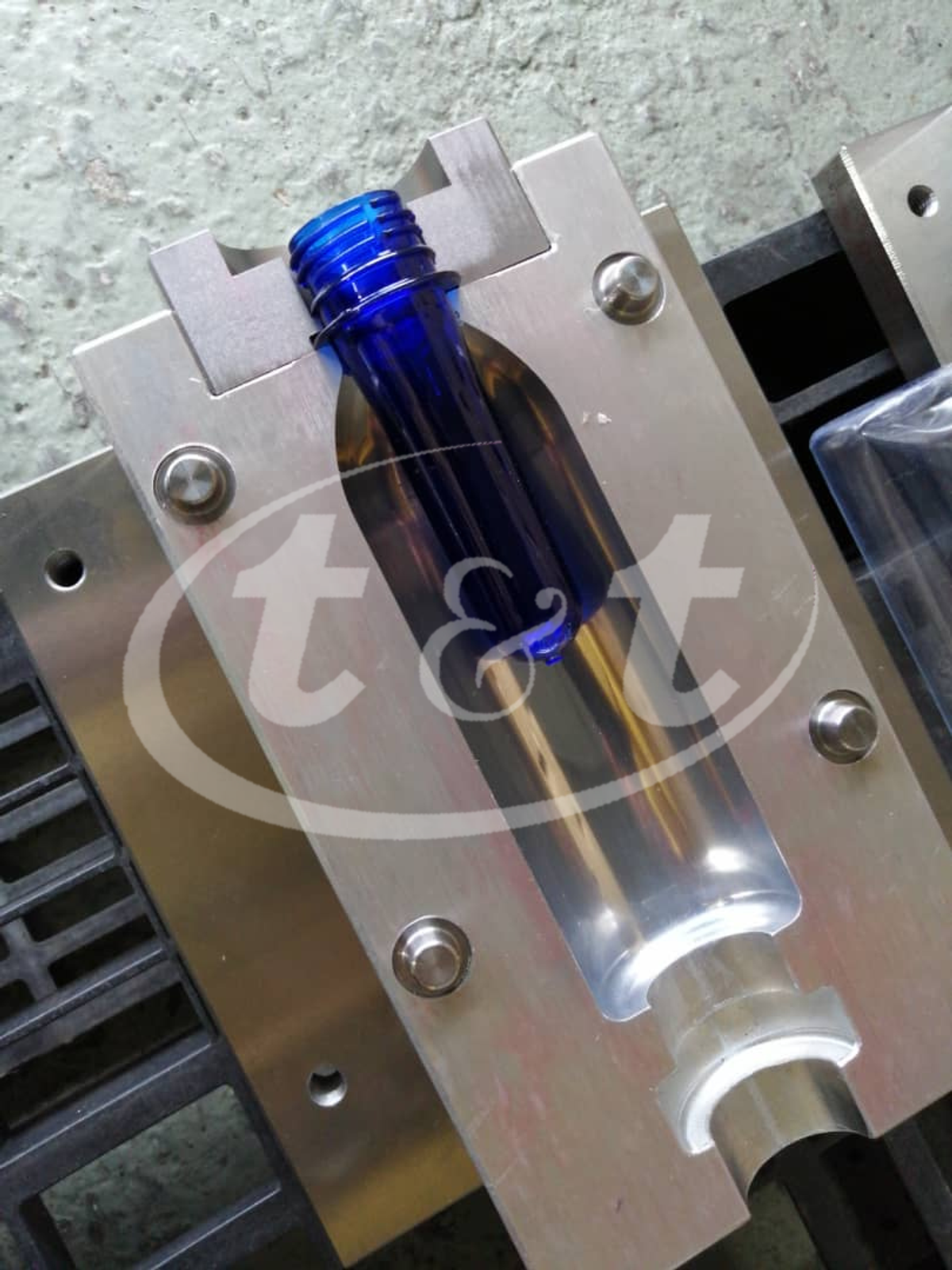
PET plastic bottles are widely used as container for drinks and beverages because they are strong and lightweight, making it ideal to be transported to other outlets safely. Other than that, clear and transparent feature of PET plastic bottles made them ideal in presenting the natural color of the drinks and beverages. Most F&B corporations have their own PET plastic bottles production lines because they design and produce their own bottles to improve their individuality and impressions. This way, they build brand recognition by making unique bottles that will catch the eyes of buyers. They will also secure returning customers through special packaging.
Generally, there are a few ways to make plastic bottles, such as extrusion blow molding, injection blow molding, stretch blow molding, injection molding and etc. We won't be going through all type of molding process because some processes are suitable for other plastic bottle such as HDPE, LDPE and etc. What we will introduce here is the type of blow molding that we used in our PET plastic bottles production: Second stage Injection Blow Molding - Bottle forming.
Injection Blow Molding
The injection blow molding actually have 2 stages: preform forming and bottle forming. Preform forming stage refers to the process where the PET flakes are being melted and formed into a preform that takes the shape of a test tube. The cooled and hardened compact preform will then be reheated and formed into PET plastic bottles in bottle forming stage. We only perform the bottle forming stage of the injection blow molding. A few processes are involved: heating, blowing and cooling.
1. Heating
The preforms are heated by passing through a tunnel with heated bulbs that will radiate temperature as high as 270°C ~ 280°C. This process ensures the preforms are heated up to a temperature where they maintain the current shape but with more softness for shaping purposes. The heats applied to the preforms are equally distributed on the body to ensure that the PET plastics will be equally distributed when compressed air is injected. Unequal heating will cause the plastic bottles produced to have parts with unequal hardness or even explode.
2. Blowing
At the end of the heated tunnel, the heated preforms will then leave the heated tunnel and placed into a mold. The mold have the shape of the bottle with desired design. Also, the inlet of the preforms are not to be changed because they comes in standard size. Only the body of the preform will be expanded and molded. Normally, there are 2 pieces of mold that will be fitted together after the preforms are placed. A core pin connected to the air compressor will then be inserted into the inlet of preform, allowing the compressed air to be blown into the heated preform. The released compressed air will have enough strength to expand the preform like a balloon. The preform will continue to expand until they touch the wall of the mold in all directions.
3. Cooling
Inside the mold, there are narrow tunnels engraved for running water at room temperature (~20°C). This will ensure that once the expanded hot preform pressed against the mold in all directions, the PET plastic will be immediately cooled down. Such cooling process will ensure that the plastic bottles formed will maintain its shape. After that, the bottles are ejected and packed accordingly.
Final words
The process looks simple because we have excluded all the adjustments and maintenance required. There are times where the preforms purchased are of different qualities and we have to make adjustments accordingly to reduce rejection rates. The rejection rates could be high due to:
a. Preform too wet (supplier failed to control the water content in PET flakes)
b. PET materials are not distributed equally on the preform
c. Heating tunnel (temperature too high or too low)
d. Wrong compressor settings
e. Mold temperature (too high, PET failed to retain shape)
f. Mold airflow
If you are planning to fabricate plastic bottles of your own design, it is advisable that you discuss with the manufacturer. Not all mold can be plug and play directly. Also, the design of plastic bottles will require experts' advice because not all designs can be realized. Over ambitious designs that lack validation will results in high rejection rates.